для получения
искусственных пленочных токопроводящих покрытий (резистов).
Сущность: краска содержит эпоксидное связующее 8-20%
наполнитель смесь графита с сажей при массовом соотношении 0,1:1,0:11-39% отвердитель 0,5-1,5% органический
растворитель остальное. Характеристика свойств: удельное сопротивление 103-104
Ом·см.
ОПИСАНИЕ ИЗОБРЕТЕНИЯ
Изобретение
относится к изготовлению лакокрасочных материалов на основе полимерных
пленкообразующих связующих и может быть использовано в различных областях
техники для получения искусственных пленочных токопроводящих покрытий
(резистов) на больших площадях поверхности изделий, предназначенных для
электротепловыделения с целью обогрева окружающей среды, например: основных и
дополнительных легкомонтируемых источников тепла жилых и производственных
помещений (теплые стены, теплые полы); оборудования для парников; сушилок для
сельскохозяйственной продукции и бытовых целей; медицинских электрогрелок;
теплых кресел для автомобилей; сухих взлетно-посадочных аэродромных полос и
т.п.
Известна
электропроводящая краска на основе полимерного пленкообразующего связующего, в
состав которой входит растворитель полимерного связующего и мелкодисперсный
электропроводный наполнитель в виде смеси серебра (60-75% от общего веса
компонентов) и графита (0,5-10% от общего веса компонентов). Пленка
лакокрасочного покрытия из известной краски после высыхания имеет удельное
объемное сопротивление порядка 103-106 Ом х см (см.
Заявку Франции N 2662703, кл С 09D 5/24, 1992). Высокое удельное
сопротивление пленки лакокрасочного покрытия объясняется тем, что несмотря на
высокое процентное содержание серебра (обладающего незначительным удельным
сопротивлением в чистом виде, порядка 1,49 х 10-6 Ом х см) в
лакокрасочном покрытии практически невозможно обеспечить непосредственный
плотный контакт мелкодисперсных смежных частиц серебра друг с другом, т.к.
указанные частицы в процессе диспергирования компонентов при изготовлении
состава обволакиваются полимерным связующим, в результате чего контакт смежных
частиц серебра в высохшем покрытии осуществляется, преимущественно, через прослойку
из материала связующего.
Наличие частиц графита
в составе способствует некоторому снижению удельного сопротивления пленки
лакокрасочного покрытия из вышеописанного состава, т.к. мелкодисперсные частицы
графита, обладая большей пористостью по сравнению с металлами (в частности
серебром), способны адсорбировать связующее и растворитель, за счет чего
обеспечивается плотный непосредственный контакт поверхностей смежных частиц
графита. Однако при наличии в составе краски частиц серебра, превышающих по своим
размерам размеры пор частиц графита, в процессе диспергирования указанные поры
будут заполняться частицами металла (серебра). В результате этого не будет
обеспечиваться плотный контакт между всеми имеющимися в пленке лакокрасочного
покрытия частицами графита. То есть и в этом случае, с учетом того, что общее
содержание частиц графита составляет незначительную часть от содержания в
составе краски частиц серебра, удельное объемное сопротивление пленки покрытия
будет лимитироваться, в основном удельным сопротивлением пленкообразующего
связующего краски, которое на несколько порядков выше, чем у графита и серебра.
Расчеты показывают,
что при получении пленки лакокрасочного покрытия из данного известного состава
на подложке в форме квадрата из диэлектрика площадью 1 м2, при
толщине покрытия 25 мкм и приложенном к соответственным участкам
покрытия напряжении 220 В (с учетом, что удельное объемное сопротивление
пленки покрытия составляет 103 Ом х см) на данном образце
будет выделяться мощность около 2 Вт.
Сравнивая эту мощность
с мощностью, например, стандартного бытового масляного радиатора (800-1200 Вт)
имеющего примерно такую же площадь тепловыделяющей поверхности, можно сделать
вывод, что известная краска не применима для ее использования при изготовлении
тепловыделяющих (резистивных) электропроводящих поверхностей нагревательных
устройств, ввиду очень высокого удельного объемного сопротивления (103-106
Ом х см) пленки лакокрасочного покрытия из известного состава. Кроме того,
электропроводящая краска известного состава является очень дорогостоящей, что
ограничивает область ее использования, преимущественно, космической и
авиационной промышленностью.
Известна
электропроводящая краска на основе полимерного пленкообразующего связующего, в
состав которой входит также растворитель полимерного связующего и
мелкодисперсный электропроводный наполнитель в соотношении 40-80% от общего
веса состава (композиции). Электропроводный наполнитель может быть выполнен из
частиц графита или углерода с содержанием 10-50% от общего веса состава
(композиции) (см. Заявка РСТ N 92-03509, кл. С 09 D 5/24, 1992).
Данная известная
электропроводящая краска, может содержать электропроводный наполнитель в виде
смеси мелкодисперсных металлических частиц и частиц графита или только в виде
графитосодержащего материала.
Недостатки известной
электропроводной краски, в которой электропроводный наполнитель выполнен в виде
смеси металлических и углеродсодержащих частиц описаны выше. То есть, в этом
случае удельное объемное сопротивление пленки покрытия из данного известного
состава будет лимитироваться удельным сопротивлением полимерного связующего и
иметь величину порядка 103-106 Ом х см, что не
позволяет использовать данное пленочное покрытие в качестве тепловыделяющего
(резистивного) элемента для электронагревательных устройств и систем.
Выполнение данного
известного состава электропроводной краски с электропроводным наполнителем в
виде одних углеродсодержащих мелкодисперсных частиц, также не обеспечит
желаемого результата, поскольку для значительного снижения удельного объемного
сопротивления пленки покрытия из известного состава требуется не только
повышение процентного содержания углеродсодержащих частиц в составе известной
краски, но и определенное процентное содержание чистого углерода в указанных частица
в совокупности с определенной удельной адсорбционной поверхностью упомянутых
углеродсодержащих частиц, что не предусмотрено в известном техническом решении.
Следовательно, получить пленочный резистор со стабильными характеристиками на
основе известной композиции (для различных напряжений в цепи источника
электропитания) практически невозможно. Кроме того, повышенное содержание
чистого углерода в известной композиции значительно снижает механическую
прочность пленочного покрытия (резиста) на основе известной композиции и,
следовательно, ограничивает область применения покрытия вследствие его малой
долговечности.
Наиболее близким
техническим решением является композиция для пленочных резистов, которая
образует резистивное покрытие со стабильными физико-механическими свойствами в
условиях воздействия повышенных температур при высокой влажности. Композиция
содержит 20-70 мас. угольного порошка, 30-80 мас. связующего
эпоксиноволака и 0,1-2 мас.ч отвердителя (имидазола) на 100 мас. ч.
связующего (см.Заявка Японии N 61-276868, кл, С 09 D 5/24, 1986)
прототип.
Недостатком известной
композиции является то, что высокое процентное содержание углеродсодержащего
наполнителя в виде угольного порошка (сажи) неблагоприятно влияет на
механическую прочность пленочных резистов из данной композиции, что
ограничивает область их использования и снижает долговечность.
В основу изобретения
была положена задача создания такого лакокрасочного состава (краски), пленочное
покрытие (резист) из которого на диэлектрической подложке обладало бы высокой
механической прочностью и низким значением удельного объемного сопротивления (от
10-3 до 10-4 Ом х см), позволяющим использовать
данное электропроводящее покрытие в качестве тепловыделяющего (резистивного)
элемента электронагревательных устройств и систем при различных напряжениях в
цепи источника электропитания и при различных условиях эксплуатации.
Поставленная цель
решается тем, что электропроводящая краска, включающая эпоксидное связующее,
углеродсодержащий наполнитель, отвердитель и органический растворитель,
согласно изобретению, содержит в качестве углеродсодержащего наполнителя смесь
графита с сажей при массовом соотношении графита к саже 0,1-1,0 при
следующем соотношении компонентов, мас. Эпоксидное связующее 8-20
Углеродсодержащий наполнитель 11-39 Отвердитель
0,5-1,5
Органический растворитель Остальное
Сочетание в
предлагаемой композиции определенного процентного содержания углеродсодержащего
наполнителя в совокупности с определенным соотношением чистого углерода (сажи)
и графита в указанном наполнителе позволяет обеспечить плотный контакт всех
частиц углеродсодержащего наполнителя в полученном из данной краски пленочном
покрытии с удельным объемным сопротивлением лакокрасочного покрытия 10-3-10-4
Ом х см, что на несколько порядков ниже, чем в известных технических
решениях. Кроме того, предлагаемое соотношение чистого углерода (сажи) и
графита в углеродсодержащем наполнителе позволяет повысить механическую прочность
покрытия на основе композиции и придать ему необходимую эластичность.
Способ получения
электропроводного лакокрасочного состава (краски) осуществляется следующим
образом.
Все компоненты (т.е.
пленкообразующее связующее, мелкодисперсный электропроводный наполнитель, и
органический растворитель) в соответствующем рецептурном соотношении загружают
в диспергирующее устройство и проводят диспергирование в соответствии с
технологически заданным регламентом. Затем содержимое разгружают и
непосредственно перед нанесением на непроводящую подложку в полученную
композицию вводят раствор отвердителя в количестве от 0,5% до 1,5% от
массы пленкообразующего связующего композиции (краски).
В качестве
диспергирующего устройства можно использовать шаровую или бисерную мельницу,
диссольвер, быстроходный смеситель. Наносить состав можно кистью, валиком, либо
пневматическим, электростатическим и безвоздушным распылением, струйным
обливом, однако наиболее предпочтительна аэрозольная технология нанесения
состава на диэлектрическую подложку.
Для получения
электропроводного лакокрасочного состава (краски) в качестве связующего
наиболее предпочтительны двухкомпонентные системы, в которых используются в
качестве связующего эпоксидные олигомеры диановой группы, т.н. диановые смолы с
молекулярной массой 400-3000. Наиболее предпочтительно использовать
эпоксидные олигомеры с молекулярной массой 400-1000. Например, марки ЭД-20
и ЭД-22 (ГОСТ 10587-93) Э-40 (ТУ 6-21-48-90), Э-41 (ТУ 6-10-3342-4-87).
В качестве
растворителя используются ароматические углеводороды, кетоны, эфиры и
хлорсодержащие углеводороды. Однако более предпочтительно использовать ацетон
(ГОСТ 2768-84), этил- и бутилацетат (ГОСТ 8991-78), этилцеллозольв (ГОСТ
8313-88), толуол (ГОСТ 9880-76), ксилол (ГОСТ 9410-78) и их
смеси.
В качестве
отвердителей используются ароматические полиамины, полиамиды, диизоцианаты и их
модификации, а также комплексы трехфторида бора, кислоты и их ангидриды. Однако
более предпочтительно использовать имидазолины и первичный, вторичный и
третичный амины. Например, полиэтиленполиамид марки ПЭПА (ТУ 6-17-12742-74)
или аминный отвердитель N 1 (ТУ 6-10-12663-77).
В качестве
электропроводящего углеродсодержащего наполнителя используется углерод (сажа) и
графит. Наиболее предпочтительно использовать, например, углерод марки П
268-Э (ТУ 38.41579-83), или углерод марки П 803 (ГОСТ 7885-86), или
графит малозольный (ГОСТ 18191-78Е), или графит порошковый особой
чистоты (ГОСТ 23463-79).
Углерод получают
термоокислительной деструкцией жидкого углеводородного сырья, такого как,
например, бензин, толуол, нафталин при температуре равной или более 1000оС.
Допускается замена
жидкого сырья газообразными углеводородами, такими как, например, этилен,
пропилен, пропан, метан или окись углерода СО. Желательно, чтобы содержание
чистого углерода в электропроводном углеродсодержащем наполнителе было бы не
менее 97 мас. а удельная адсорбционная поверхность более 230 м3/г.
Частицы графита имеют
разветвленную форму (структуру), их преимущественные размеры 0,3-30 нм,
что повышает эластичность пленочного покрытия на основе предложенной композиции
(краски).
Составы композиций
конкретных электропроводящих красок представлены в таблице.
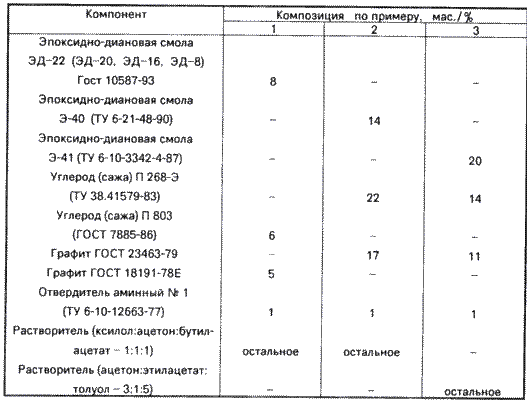
1-й пример
(см.табл.) состав
композиции для получения пленочного электропроводящего покрытия, используемого
при подводимом напряжении 12 В.
2-й пример
(см.табл.) состав
композиции для получения пленочного электропроводящего покрытия, используемого
при подводимом напряжении 110 В.
3-й пример (см.
табл. ) состав
композиции для получения пленочного электропроводящего покрытия, используемого
при подводимом напряжении 220 В.
Экспериментально
проверено, что в каждом из вышеуказанных примеров соответствующий качественный
и количественный состав электропроводящих красок при заданном значении
подводимого напряжения обеспечивает температуру нагрева пленочного покрытия
(образуемого данным составом) в пределах от 30 до 100оС.
Таким образом,
основными преимуществами предлагаемого состава краски является то, что
получаемое на его основе пленочное электропроводное покрытие на диэлектрической
подложке обладает следующими свойствами:
низкое удельное сопротивление (от 10-3 до 10-4 Ом х см),
позволяющее использовать как безопасные (12-36 В), так и промышленные (127-220
В) значения напряжений при использовании лакокрасочного пленочного покрытия
в качестве тепловыделяющего (резистивного) элемента электронагревательных
устройств и систем;
высокая адгезионная способность, позволяющая использовать широкий спектр
подложек, включая стекло, слоистые пластики, резину;
возможность создания нагревательных поверхностей большой площади;
возможность в процессе изготовления получать электротепловыделяющие пленки с
заданным выходным температурным параметром в интервале температур 30оС-300оС;
экономичность;
возможность изготовления электротепловыделяющих пленок с тепловой нагрузкой от
150 до 1600 Вт/м2;
оптимальные условия теплопередачи получаемых электротепловыделяющих пленок. |